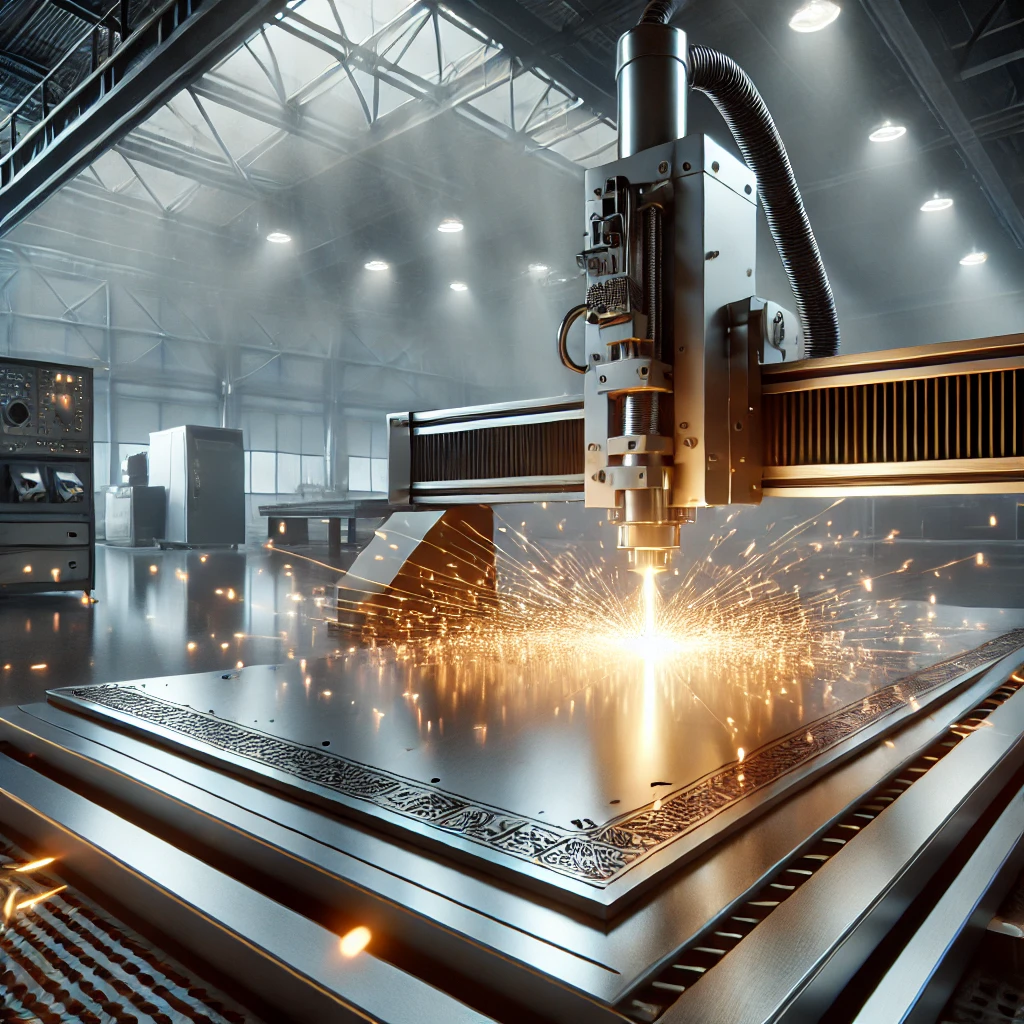
Introduction
In the industrial world, metal cutting is more than just a process; it’s an art and science that impacts many sectors, from automotive to aerospace. The demand for precise and efficient production methods is growing exponentially. As a result, mastering techniques like metal cutting has become crucial in ensuring that materials are shaped to perfection, meeting stringent industry standards and expectations. The significance of metal cutting in our modern industrial landscape cannot be overstated, and it’s the backbone of countless manufacturing processes.
With technological advancements, metal cutting is no longer confined to traditional methods. Modern techniques have emerged, offering enhanced precision and efficiency, redefining the possibilities of shaping metal, as shown in https://bluegrassbit.com/services-we-offer/metal-cutting/. Understanding the intricacies of these methods is critical to leveraging their full potential and achieving outstanding outcomes in a competitive marketplace.
The Basics of Metal Cutting
Removing material from a metal workpiece to shape it according to specific design specifications is known as metal cutting, and it is an essential industrial operation. Common materials used include steel, aluminum, and titanium, each with unique properties influencing the cutting process. Understanding the mechanics of metal cutting, including shearing and machining, is essential for professionals to produce components that meet precise specifications and rigorous quality standards. Mastery of these processes is crucial for professionals across industries.
Techniques Used in Metal Cutting
Metal cutting involves various techniques, each with its advantages and limitations. Traditional methods like sawing and shearing are used for simple tasks, while laser and plasma cutting have expanded possibilities. Laser cutting is known for its precision, allowing for intricate designs and thin materials. Plasma cutting is ideal for heavy-duty applications, slicing through thicker metals. Understanding these techniques helps industries select the most suitable method for their specific needs, ensuring efficiency and effectiveness in their operations.
Emerging Technologies in Metal Cutting
Metal cutting has seen significant technological advances, particularly with the introduction of CNC (Computer Numeric Control) machines. These systems automate and precisely control cutting processes, reducing human error while enhancing precision and repeatability.
Emerging technologies such as CNC machining represent a paradigm shift in the industry, where autonomy and precision are becoming the norm rather than the exception. These advancements underscore the critical importance of embracing technological innovations to maintain competitive advantages in manufacturing.
Advantages of High Precision in Metal Cutting
Precision in metal cutting is crucial for complex assemblies in high-tech industries. It ensures perfect component fit, reduces material wastage, saves costs, and minimizes environmental impacts. Case studies across sectors show significant improvements in product quality and cost efficiency. Precision directly impacts the functionality and aesthetics of the end product, making industries that prioritize it better positioned to meet evolving clientele and industry standards.
Challenges and Solutions in Metal Cutting
Professionals in the metalworking industry face numerous challenges, ranging from tool wear and tear to material selection. Overcoming these hurdles often requires adopting innovative solutions and embracing the latest technologies. Insights into overcoming manufacturing challenges illustrate how industries adapt to keep pace with evolving demands and maintain efficiency in their operations.
Solutions to these challenges often involve advancements in tool coating technology, improved cooling techniques, and enhanced machine calibration. By staying at the forefront of such innovations, manufacturers can mitigate common obstacles and maintain optimal productivity.
Factors Influencing the Choice of Cutting Method
Choosing the appropriate metal cutting method involves considering various factors, including the material type, thickness, required precision, and production volume. Every one of these elements is crucial to the decision-making process:
- Material Type: Different metals react differently under heat and pressure, necessitating unique handling approaches.
- Thickness: Determines whether laser or plasma cutting is more appropriate, as each method has its own optimal application range.
- Precision: High precision demands technologies like CNC or laser cutting, ensuring tight tolerances and fine details.
- Production Volume: Higher volumes might benefit from automation technologies, enabling rapid and repeatable operations.
Understanding these elements provides a foundation for selecting an optimal technique tailored to specific industrial needs, promoting efficiency and quality in manufacturing.