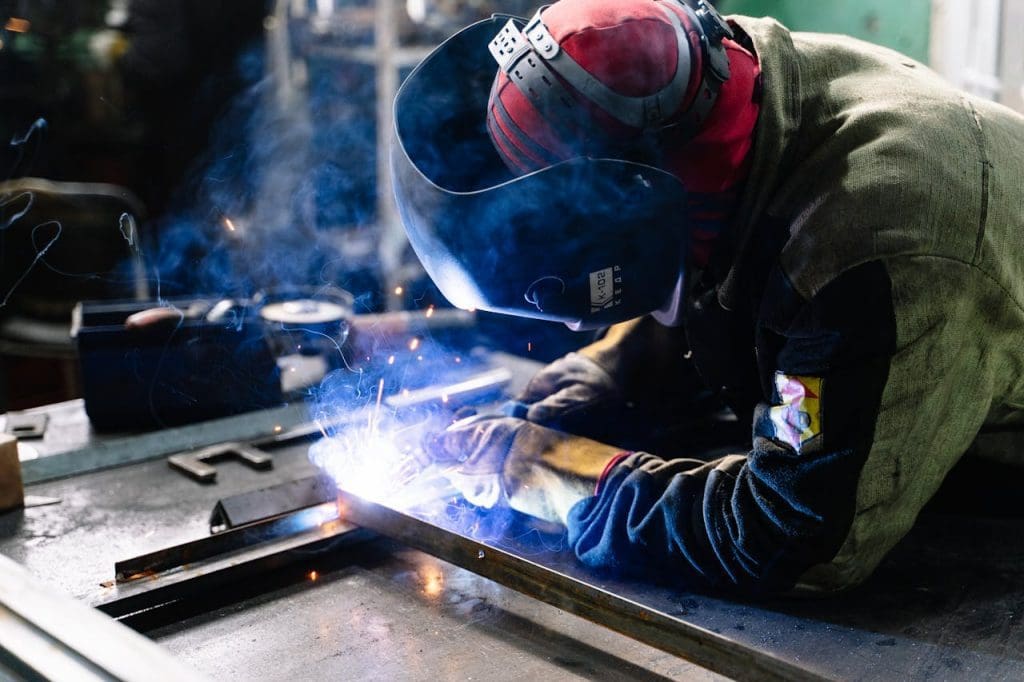
Working with metals is both empowering and exciting. As the heat turns up and sparks fly, welders can transform the world’s strongest metals or materials into products and shapes they envision. These skills need practice and work to acquire, and it will always be a good idea to learn with the guidance and assistance of industrial experts. Learning all the ropes of the new trade can take time. According to experts at Micro Weld, you have to familiarize yourself with the whole working process from beginning to finish and, at the same time, master different types of welding, including the following:
1. TIG Welding
Tungsten inert gas welding or precision TIG welding produces high-quality welds and remains versatile. This form of welding is used for more complex and larger projects that require more control. Although the welding procedure produces good results, it requires more training and takes a lot of time to master.
2. MIG Welding
This is among the simplest forms of welding that beginners can start with and learn. MIG welding involves two different forms of welding. The first one uses bare wire, while the second uses flux core. Bar wire joins thinner metal pieces, whereas flux core is used outside as it doesn’t need a gas supply or flow meter. Generally, MIG welding is the process of choice for hobby welders and DIY enthusiasts with no cash to spend on costly equipment.
3. FCAW (Flux Core)
Flux-cored arc welding (FCAW) combines affordability, speed, and portability. It is suitable for offering industrial welding services, like conducting generator repairs, fabricating on construction sites, welding outdoors, and working with very rusty materials. It is similar to MIG welding but doesn’t require shielding gas. Other welding methods require gas that helps to protect weldment against contamination. During the FCAW process, machines feed electrodes filled with ‘flux’ protecting the arc. This explains why this method is more portable and suitable for use outdoors.
4. Laser and Electron Beam Welding
This welding process involves fusing two metals using a laser or a beam of electrons. The resulting welds are quality and precise. Laser and electron beams often happen inside a unique and vacuum atmosphere. This environment ensures everything remains stable for electrons to do their work. Industries, such as car manufacturing and aerospace, depend on this welding.
5. Gas Welding
Although TIG welding has replaced it, some people prefer using gas welding. Do you know why? It is suitable for joining ferrous and non-ferrous metals. Acetylene and oxygen are essential for welding kits, which are portable and don’t require electricity. Its users report that the method excels in fusing metals such as copper, aluminum, and steel. This versatility makes it a suitable option in various industries, including metal sculpture and automotive repairs, where controlled heat and precise application are required. Gas welding is also used in the following:
- Maintenance
- Artistic metalwork
- Plumbing
6. SMAW (Shielded Metal Arc Welding)
This welding process depends on manual techniques using consumable electrodes coated in a flux. The method is popular among many home-shop welders. SMAW is called stick welding because the electrodes used to weld metals come as sticks. Since the process needs minimal equipment, SMAW remains a cost-effective method. It works perfectly well on rusty and dirt materials.In conclusion, different welding methods help to join together various materials. The type of method depends on the size and thickness of the material you want to weld and the kind of finish you need.